Commercial Ice Machine Troubleshooting: Identify & Fix Common Issues Quickly
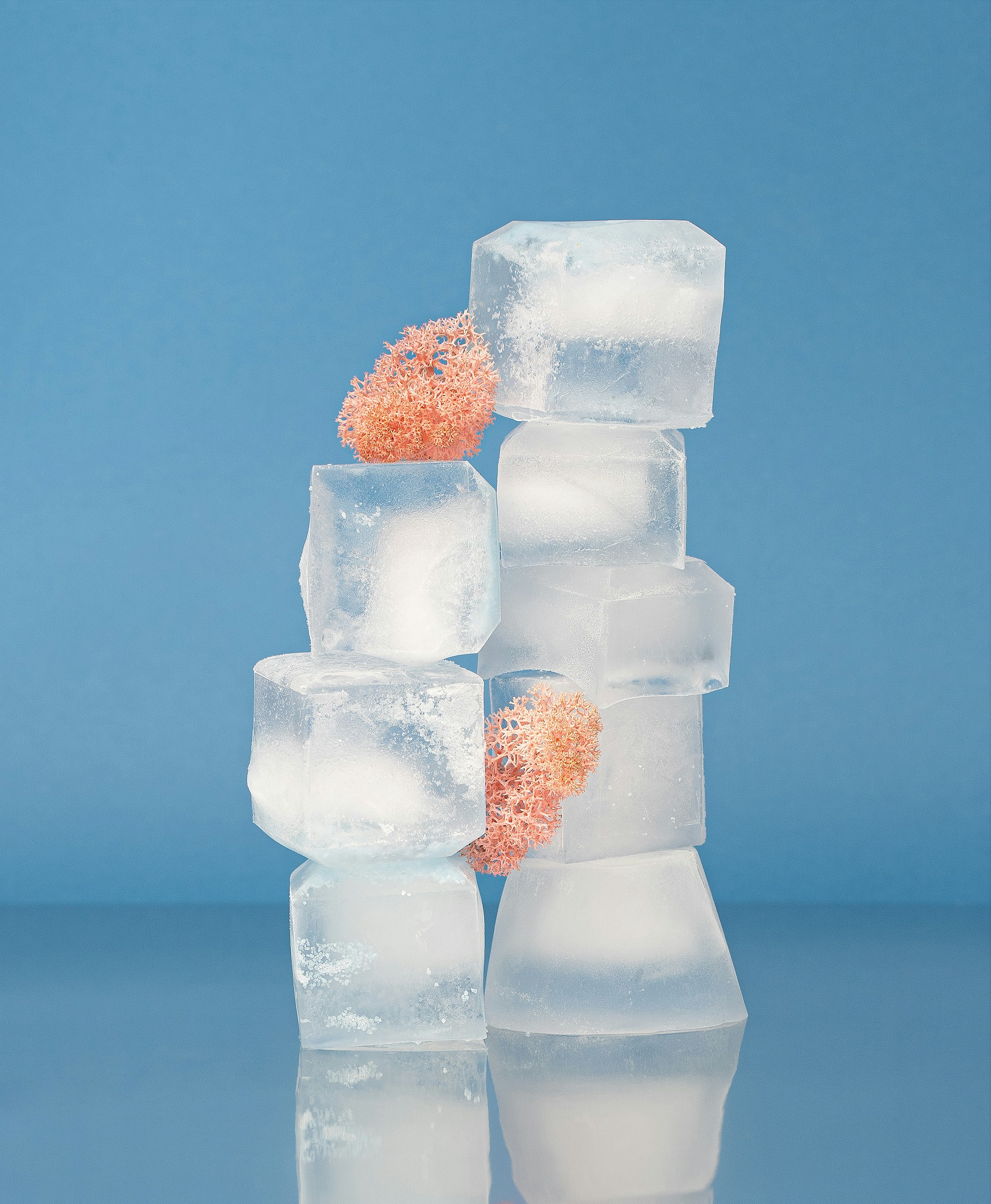
A commercial ice machine is an essential piece of equipment in any restaurant, bar, or food service operation. When it malfunctions, it can disrupt operations, lead to unsanitary conditions, and result in lost revenue. Knowing how to troubleshoot common ice machine issues can help you minimize downtime and avoid costly emergency repairs.
This guide provides a structured approach to identifying and resolving common ice machine problems. It will help you determine which issues can be fixed in-house and when it’s time to call a technician. Additionally, we’ll cover essential tools, best practices, and how to maintain your ice machine efficiently to prevent recurring issues.
1. Common Symptoms and Possible Causes
Understanding the warning signs of an ice machine malfunction can help you take immediate action before the issue escalates. Below are some of the most frequently encountered problems and their potential causes.
🧊 Ice Production Problems
When your ice machine is not producing ice efficiently, it can impact service quality and customer satisfaction.
- Machine not making ice – Possible causes: Clogged water filter, malfunctioning water inlet valve, or thermostat issues.
- Ice is too thin or too soft – Possible causes: Low water pressure, dirty evaporator plates, or incorrect machine settings.
- Ice is too large or too hard – Possible causes: Calibration errors, excessive freeze cycle, or high mineral content in water.
- Ice machine is slow to produce ice – Possible causes: Dirty condenser coils, insufficient refrigerant, or high ambient temperature.
- Ice cubes sticking together – Possible causes: Inconsistent water flow, faulty sensors, or overly long freeze cycles.
Regular monitoring and quick intervention can prevent these issues from leading to downtime.
💦 Water Leakage & Humidity Issues
Excess moisture or leaks can create unsanitary conditions and damage surrounding equipment.
- Water leaking from the machine – Possible causes: Clogged drain, loose water supply connections, or damaged water inlet valve.
- Excess condensation or water pooling near the machine – Possible causes: Poor ventilation, drain blockage, or high humidity in the environment.
- Ice melting too quickly in the bin – Possible causes: Malfunctioning bin thermostat, improper air circulation, or a faulty door seal.
- Water filter clogging frequently – Possible causes: Poor water quality, old or incompatible filters, or high mineral content.
Addressing these issues promptly will maintain hygiene standards and ensure smooth operation.
⚠️ Electrical and Mechanical Issues
Power supply problems or mechanical failures can bring your ice machine to a halt.
- Ice machine won’t turn on – Possible causes: Power supply issues, tripped circuit breaker, or faulty internal wiring.
- Loud or unusual noises – Possible causes: Loose fan motor, ice buildup on moving parts, or compressor issues.
- Evaporator or condenser coils freezing up – Possible causes: Thermostat failure, refrigerant leaks, or restricted airflow.
- Machine short-cycling (turning off and on frequently) – Possible causes: Malfunctioning sensors, dirty air filters, or overheating components.
Being aware of these common failures allows for proactive solutions that prevent complete breakdowns.
2. Quick Fixes: What You Can Do Yourself
Not every issue requires a technician. Some problems can be addressed in-house with simple troubleshooting steps. Below is a guide to diagnosing and fixing common issues.
Machine not making ice
- Check if the water filter is clogged and replace it if needed.
- Inspect the water inlet valve for blockages.
- Ensure the thermostat is set correctly.
Ice is too soft or too thin
- Verify the water pressure to ensure it meets manufacturer guidelines.
- Clean the evaporator plates to remove buildup affecting ice formation.
Water leaking from the machine
- Tighten any loose water supply connections.
- Inspect the water inlet valve for potential damage.
- Clear out any clogs in the drainage system.
Ice melting too quickly in the bin
- Test the bin thermostat and replace it if faulty.
- Improve air circulation around the machine to reduce ambient heat.
Unusual noises coming from the machine
- Check if the fan motor is loose or damaged and tighten components.
- Look for ice buildup on moving parts and remove excess ice manually.
Ice cubes sticking together
- Adjust the freeze cycle time to ensure ice formation is consistent.
- Inspect the water flow to ensure it is properly regulated.
Additional Troubleshooting Tips:
✔ Clean the condenser coils – Dirt and grease buildup cause inefficiency and overheating.
✔ Check water supply lines – Ensure no blockages or kinks are reducing water flow.
✔ Inspect for ice buildup – Manually remove excess ice if needed and defrost frozen parts.
✔ Test thermostat settings – Adjust to the recommended manufacturer settings.
✔ Reset the machine – Power cycling the unit can resolve many minor glitches.
✔ Check air filters – Dirty air filters can restrict airflow and reduce efficiency.
By following these steps, you can resolve minor issues before they escalate into major repairs.
3. When to Call a Technician
While some troubleshooting can be done in-house, certain issues require professional expertise to avoid further damage or costly repairs. Calling a technician at the right time ensures that problems are properly diagnosed and resolved before they become critical.
Signs You Need a Technician
❌ Repeated malfunctions – If the same issue keeps occurring despite troubleshooting.
❌ Electrical failures – If the machine isn’t receiving power and resetting doesn’t help.
❌ Refrigerant leaks – Requires professional handling due to safety concerns.
❌ Unusual odors or mold growth – Indicates deep-seated contamination that needs professional cleaning.
❌ Damaged internal components – If major parts like compressors or evaporators need replacement.
❌ Sensor or control panel failure – If settings are not responding correctly.
Finding a reliable technician can be challenging, and coordinating multiple maintenance appointments can be time-consuming. That’s where Boh can help—by connecting you with qualified professionals who handle repairs and routine maintenance, ensuring your ice machine stays in top condition with minimal effort on your end.
4. Essential Troubleshooting Tools
Before diving into troubleshooting, it’s crucial to be equipped with the right tools. A well-stocked maintenance toolkit ensures that minor issues can be quickly diagnosed and resolved without the need for immediate professional intervention.
🔧 Thermometer – For checking ice storage temperature and water temperature.
🔧 Multimeter – To test electrical connections and diagnose power issues.
🔧 Soft-Bristle Brush – For cleaning evaporator plates without causing damage.
🔧 Sanitizing Solution – To ensure proper hygiene after handling the machine.
🔧 User Manual – Always refer to the manufacturer’s guide for specific troubleshooting steps.🔧 Compressed Air or Small Vacuum – To remove dust from vents and cooling components.
Using these tools regularly can help you detect and address potential problems early, preventing larger breakdowns that require costly repairs.
Conclusion: Proactive Maintenance Saves Time and Money
Troubleshooting commercial ice machine issues can help minimize downtime and prevent costly repairs. By recognizing common symptoms, performing quick fixes, and knowing when to call a technician, restaurant owners can ensure their ice machines remain efficient and hygienic.
However, regular maintenance is the key to avoiding frequent breakdowns. Implementing a preventive maintenance schedule and leveraging professional services ensures long-term reliability.
✅ A well-maintained ice machine runs efficiently, produces high-quality ice, and reduces unexpected breakdowns.
👉 Need an easier way to manage ice machine maintenance? Boh simplifies scheduling, servicing, and technician coordination so you can focus on running your restaurant smoothly.
By taking proactive steps, restaurant owners can ensure that their ice machines stay in peak condition, minimizing repair costs and maximizing operational efficiency.